Automated Machine Guidance
3D design models streamline the development of automated machine guidance (AMG) construction models to ensure consistency with the project design. Data exported from 3D models is transferred to global positioning system (GPS) or local positioning systems (LPS) machine control equipment that guides and directs construction equipment such as cold planers, pavers and rollers. The connectivity allows the most accurate, up-to-date models to be received, even if mid-cycle design changes are made.
Grades, cuts and fills are constructed to a high level of precision on the first pass either automatically or with the guidance of an onboard system. First-pass accuracy of AMG equipment reduces waste and economizes resources by reducing labor, equipment idle time and rework. This results in a reduction of fuel consumption and greenhouse gas emissions by up to 40 percent at a faster project completion with improved quality and safety. Automation also decreases the need for certain tasks like staking, stringing lines, drawing fill lines and setting grade stakes, again reducing labor and increasing project safety.
To Learn More About 3D Modeling
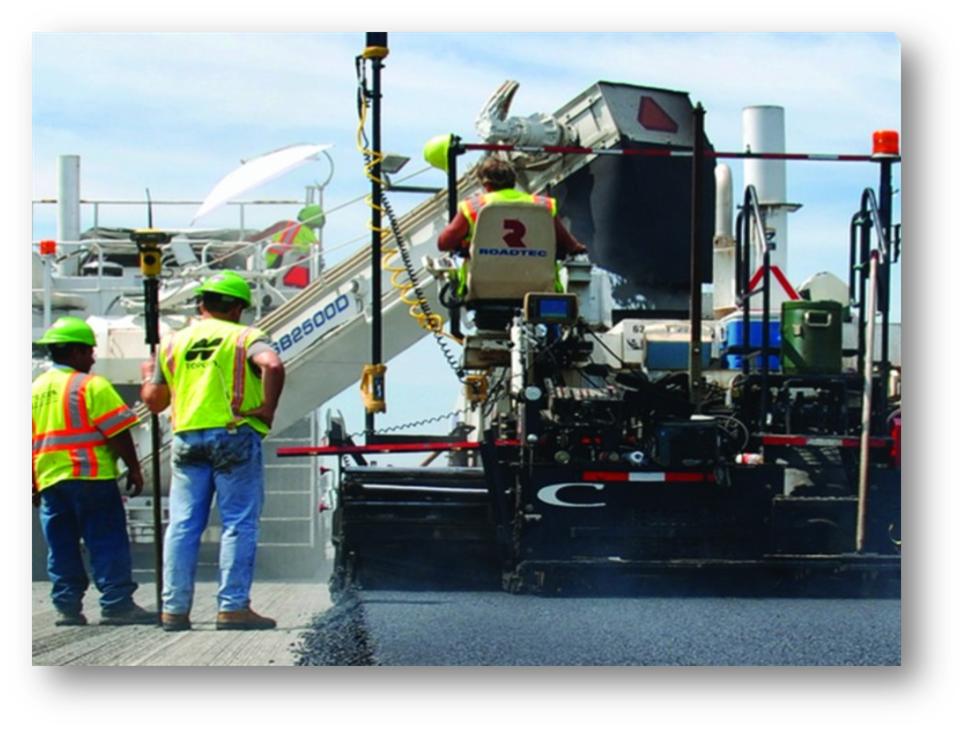
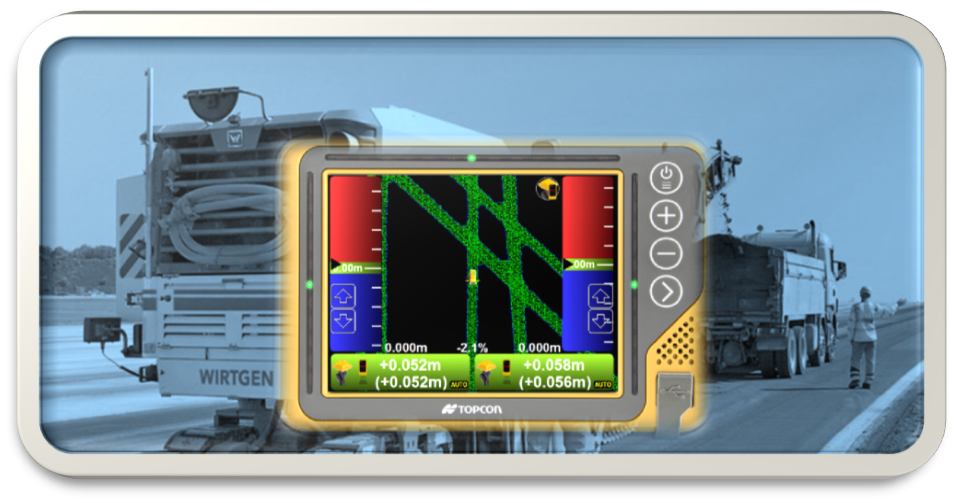
3D Systems
There are a variety of systems which allow for 3D modeling and machine control. Most commonly are LPS or a combination GPS/LiDAR scanning point cloud system.
- LPS (Local Positioning System)
An LPS uses a physical connection to make corrections to positional data. These systems include total station or millimeter GPS.
LPS is the most accurate measurement, grade checking and machine control technology available because it uses line of sight to a fixed controlled point for referencing for grades and machine positioning. During 3D machine control, LPS typically requires one transmitter and control point per receiver for referencing control for each piece of equipment. In addition, there must be an adequate number of control points to maintain line of sight throughout the entire project for any system referencing control. This results in a system that is cumbersome for large projects because the area which can be covered for one control point is not very large, typically limited to a distance of approximately 1,200 feet between transmitters. It is ideal for new construction projects where elevation control is critical and for multiple lift operations since one surface model can be used.
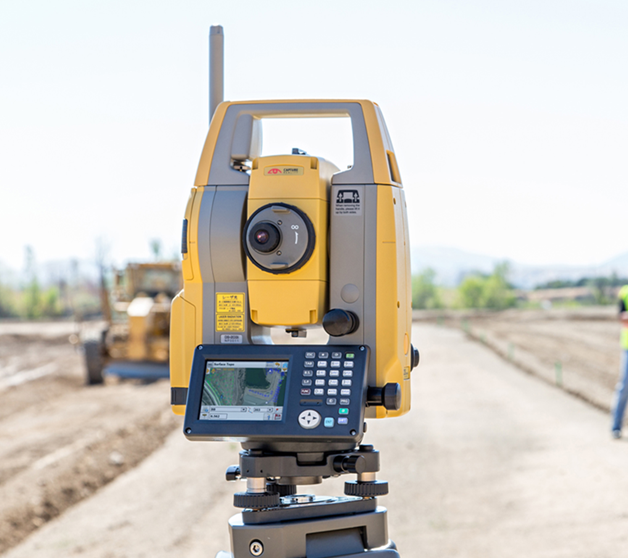
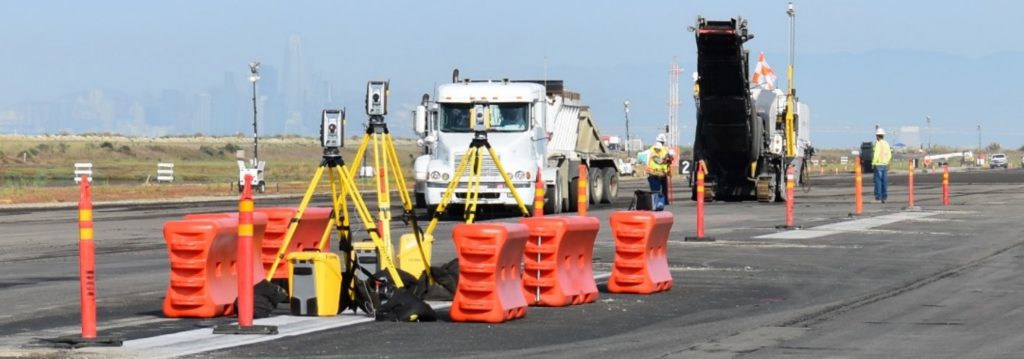
- GPS/LiDAR (Global Positioning Systems/ Light Detection and Ranging) Scanning
GPS and a truck mounted LiDAR scanner are used to collect millions of points to generate a point cloud and create a 3D scan and visual of the entire surface. These points use GPS for horizontal position and relative reference for vertical position data across the entire scanned surface. The scanning can be conducted in live traffic. No traffic control is required, making it ideal for rehabilitation projects.
Once the data has been collected, a 3D design model referencing the existing surface can be created for optimal final surface results. The model can then be used for 3D machine control to ensure the design is constructed with precise accuracy using relative depth referencing. A single model cannot be used for multiple lifts. A new model is required for each lift surface or if the scanned surface has changed significantly. The significant advantages over LPS, besides the ability to scan in live traffic, is that multiple pieces of equipment can be controlled by the same model. Length of control within a project is approximately 2 miles in both directions from a single GPS correction signal such as an onsite base station or of unlimited length when using a network RTK correction signal.
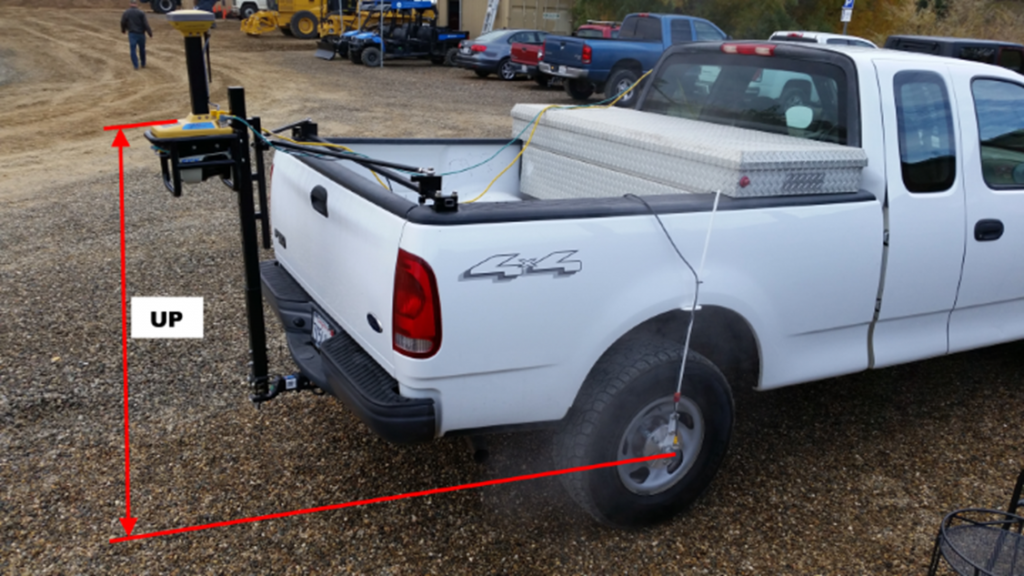
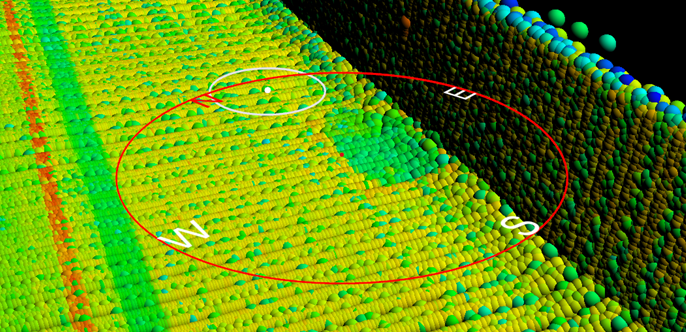