The roughness or smoothness in paving a roadway is based upon:
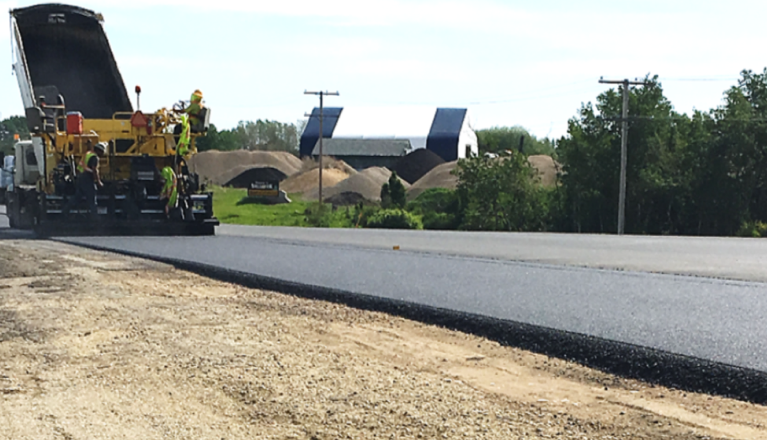
Variable Depth Paving & Cold Planing
Unless the surface to be paved with an overlay or to be cold planed and overlaid is already smooth, variable depth cold planing and/or paving will be required to improve smoothness. Constant depth cold planing will essentially transfer the roughness of the existing surface to the bottom of the cold planed surface. Constant depth paving will transfer the roughness of the existing surface to the top surface.
Variable depth paving improves smoothness, but it may also result in deferential compaction when using two-dimensional (2D) paving grade control systems. This can be minimized by using 3D automated machine guidance paving where the amount of loose material placed prior to compaction is automatically adjusted to compensate for differential compaction thicknesses.
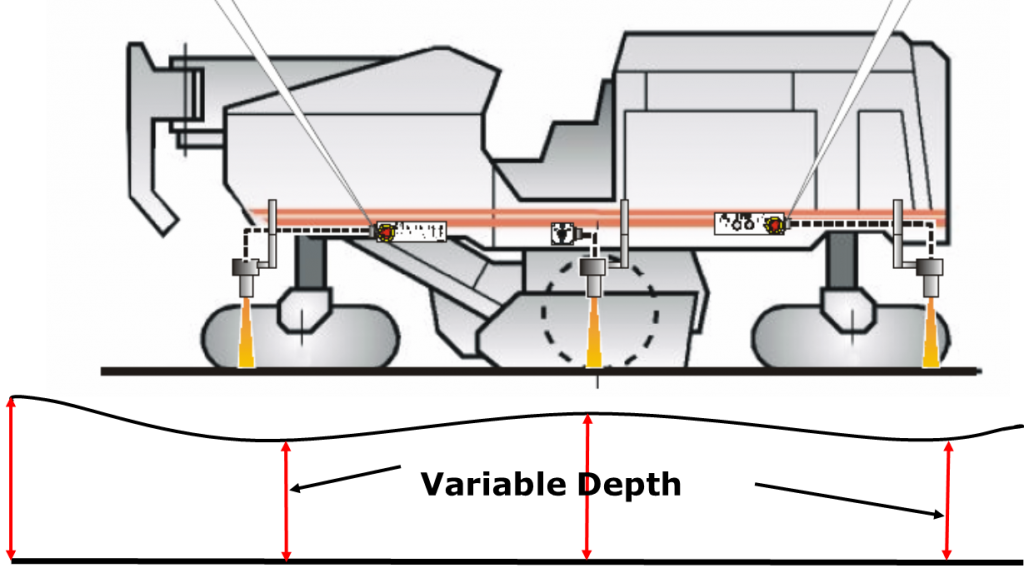
Another way to avoid differential compaction during paving is to “profile” the road with variable depth cold planing prior to paving. When the finished cold planed surface is at the desired smoothness, 2D constant or minor variable depth paving can be used.
Thickness Control
A cold planer’s head height changes directly using a 2D automatic control referencing system or 3D automated machine guidance. A free-floating screed of a paver is attached to a tractor unit by tow points. Hydraulic cylinders move the positions of the tow points either by manual control, 2D automatic control referencing or 3D automated machine guidance.
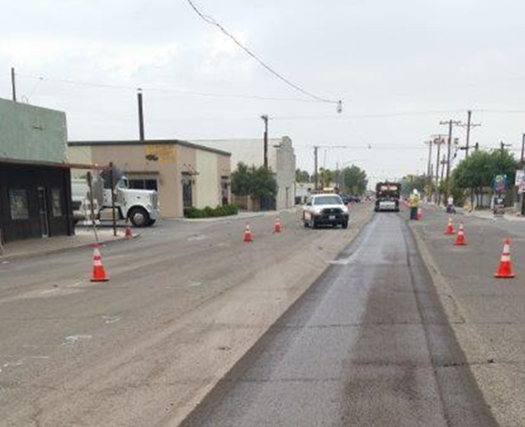
-
Manual Screed Control
Manual adjustments for a paver should be a last result. The ability to produce a consistently smooth mat depends on the frequency with which the operator adjusts the screed. If a second thickness change is made before a first change has been completed, the first change will not be completed since it takes 5 times the length of the tow arm (typically 50 feet, 15 m) to compete an adjustment. It is virtually impossible for a manual operator to control a screed as smoothly as an automatic system can.
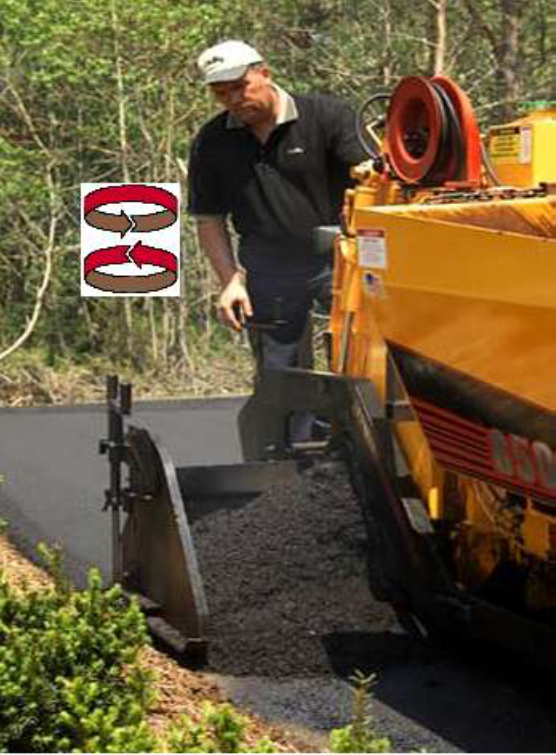
-
2D Automatic Control Reference Systems
2D automatic control referencing systems, if properly setup, improve smoothness compared to the reference surface. Grade reference systems can be used alone on either side of a paver or cold planer, or on both sides of a paver or cold planer simultaneously. There are three types of 2D grade control reference systems.
-
-
String Line
The control of the paver thickness is made by referencing a preset string line, providing it is taunt, smooth and long. A sag in the line will cause a dip in the mat beyond the sag due to the response time of the paver. Due to the time and labor it takes to setup a string line, they are more commonly used on new construction then on rehabilitation paving projects. A string line is not commonly used with a cold planer.
-
-
-
Joint Matching Shoe
A joint matching shoe on a paver or cold planer follows the existing surface in which it rides. It should only be used if the pavement surface it matches is smooth. A joint matching shoe can be either mechanical or sonic.
-
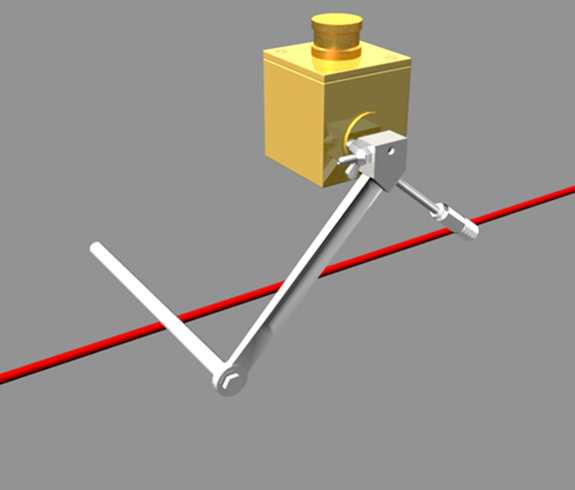
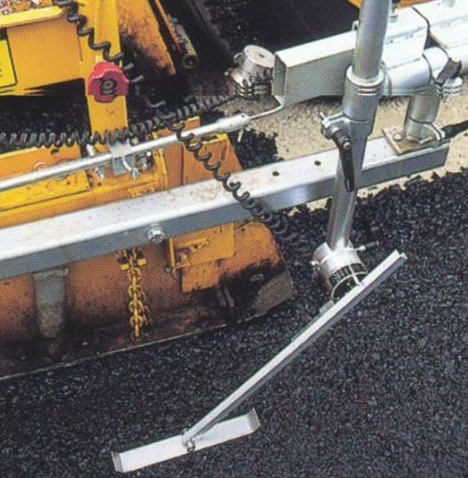
-
Skis
Skis are 2D grade control systems that average the existing roughness on the referenced surface to provide the best smoothness. The averaging is limited to the length of the ski, typically 20 to 40 feet (6 to 12 m). There are two types of skis: Mechanical/Contact and Non-Contact.
-
-
Mechanical Skis (Contact)
A floating beam with a series of shoes attached to the bottom of the beam ride on the surface it is referencing. The grade sensor reads off a wire attached to each end of the beam or it is attached directly to a grade referencing beam.
-
-
-
Non-contact skis
Non-contact work like mechanical skis, except they ride in the air using three to four sensors that are electronically connected to produce a continuous averaging beam. They use sonic for referencing.
-

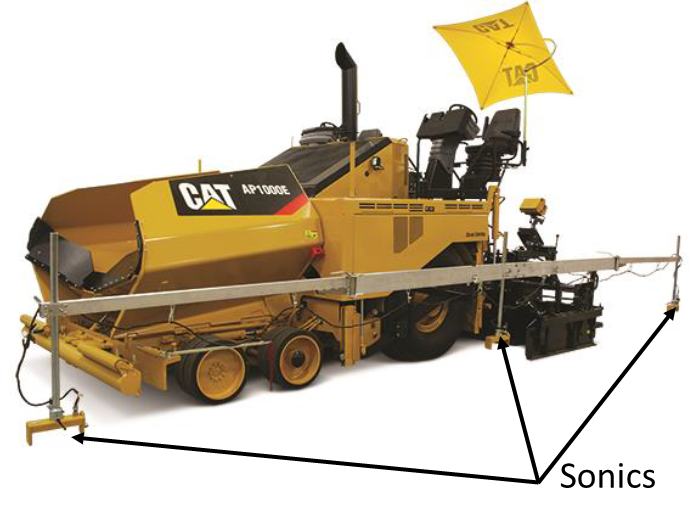
-
Slope Control
Slope control is accomplished by running a grade control system on one side of the paver or cold planer and then setting the thickness on the other side via a constant slope. Slope control should be run inside-out and not outside-in. Grade control should not be on the outside with slope control in as this may provide a poor inside joint to match.
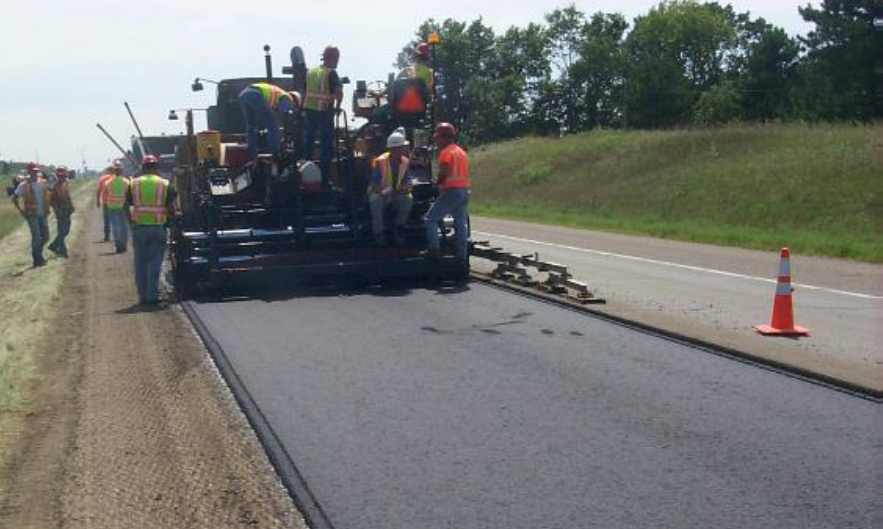
-
3D Automated Machine Guidance Systems
Using 3D automated machine guidance systems, cold planing depth or paving thickness is constructed to a high level of precision on the first pass automatically. Essentially, the cold planing cut or paving surface thickness are constructed based upon a 3D model that uses virtual skis of user defined lengths or designed straight line slopes and grades.
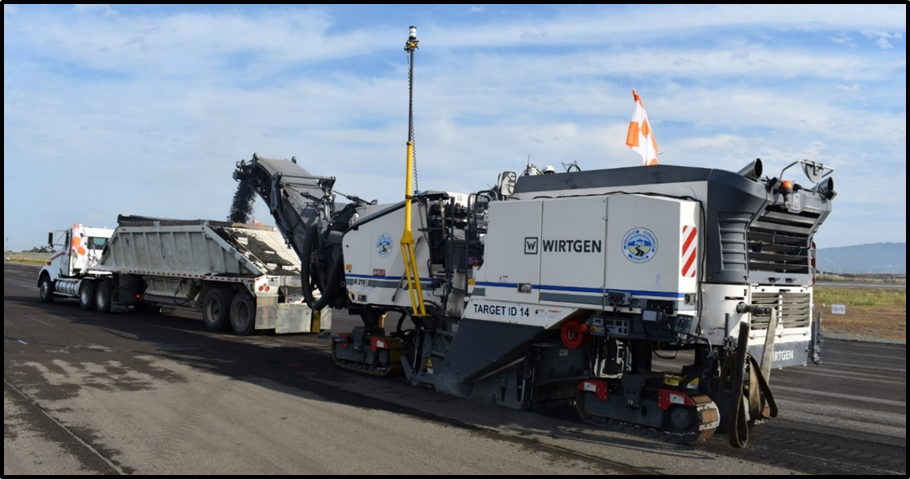
Variability in Paving Conditions
The Golden Rule of paving smoothness is that CHANGE IS BAD! And NO CHANGE IS GOOD! To achieve smoothness is to maintain consistency at all stages of the paving operation. Beyond thickness control, other factors that control the ability of the screed of a paver to place a level and smooth surface are:
- Control of the Head of Material in Front of the Screed
If the head of material against the screed fluctuates widely during paving it is difficult to produce a level and smooth pavement surface. Increased material will result in more resistance against the screed, resulting in a depth increase. Decreased material causes less resistance, resulting in a depth decrease. A constant head of material results in a constant depth placed.

- Variability in Speed of Paving
In order to maintain smoothness, the paver operation should be continuous (no stopping) and at a constant speed. As the paver speeds up it will temporarily change the angle of attack of the screed and more mix must be delivered to keep a constant head. If not, increasing the paving speed will cause less resistance and the screed will drop resulting in a depth decrease. The effect of a rapid reduction of a material head is a dip. However, if material is rapidly fed to the augers to compensate, the screed may have more resistance against it resulting in a bump. As the paver is slowed, the resistance of the screed against the head of material will increase causing the screed depth to increase.
.jpg)
- The more abrupt the speed change the more impact to the paving surface. If the paver speed changes, the feed rate should change proportionally to maintain a constant head of material. When the material is out of balance with a fluctuation of material it could cause a low spot-bump-low spot-bump, etc.
- Paving speed should be optimized by using Delivery Monitoring and Automated Ticketing. Based upon feedback, the optimal paving speed is based upon:
-
- – Plant production rate
- – Number of trucks, yield and cycle times
- – Efficiency of truck ingress and egress to paver loading
- – Compaction time
- – Available traffic control
- – Mix temperature
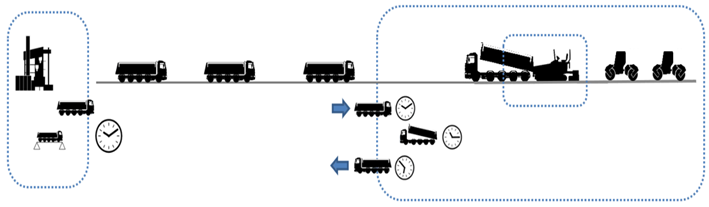
-
Paver Stops
Any stopping of the paver will cause screed settlement due to the weight of the screed. It will also cause roughness due to the change of paver speeds into and out of the stop. Depending on the time of the stop, compaction may be more difficult to achieve because the mix has cooled in the area of the paver stop. Paver stops can be are monitored with Paver Mounted Thermal Profiling and can be minimized with Delivery Monitoring and Automated Ticketing.
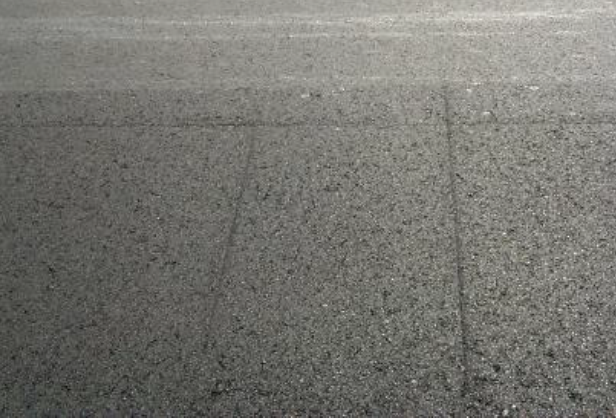
- Mix Temperature Uniformity
Variation in mix temperature can result from a variety of ways including:- – Plant operations
- – Trucking operations
- – Segregation during loading of the trucks and paver
- – Wind and ambient temperature variations
- Any variation in mix temperature needs to be minimized so that the screed will remain consistent for the smoothest pavement possible. Cooler mixes are stiffer than hotter mixes and increase the force acting on the screed causing the screed to rise and increasing thickness. Hotter mixes cause the screed to drop due to the reduced resistance on the screed. Cooler mats may not achieve the same density as hotter mats at the same rolling pattern, thus resulting in deferential compaction. Thermal segregation due to trucking and paving operations or due to material segregation may also result in differential compaction. Paver Mounted Thermal Profiling effectively monitors thermal segregation and material temperature behind the paver screed.